Manoj Sivaraman
Member
Hi audiophiles and fellow members, I'm Manoj Sivaraman being a DIY guy I love to fabricate, assemble and make things on my own.
After building a DIY optical 5.1 channel receiver (please make sure to check out my entire build on the DIY section). I'll add this build plans for you guys if you wish to build similar ones.
So without much into let's jump into the build...
The quest continued as I needed a floor stand to properly install my rear surround channel as my living room wasn't planned to house surround speakers including wiring.
Went on for nearby shops the starting price for stands were about 600-700 per stand.
I felt for that price the build and quality could have been better and my speakers were quite heavy for the given small dimensions. It weighs around 600-700grams being just a 3inch and a tweeter with heafty two way diy crossover.
Mine wasn't well balanced on those stands. The stand shakes and it's barely standing a slight touch could tip things over.
So thought of building my own
The idea bulb was lit:
Saw some YouTube videos where I came across some decent builds
So with a simple build idea I went on to local metal scrap place.
And calculated the price of required Stainless steel channels
It came out to be a costly option and seems to be pretty hard to work with as I need to get things welded(again having a small welding machine, but lazy to work with).
So thought why not to use something light yet string and balance the speakers properly.
The Discovery:
Yes,The discovery CONCRETE!!!!!
Went to a nearby restaurant where I saw raw finished concrete brick wall finished with varnish.
So got the idea of having concrete as my base and aluminum as stands.
Went to nearby construction blue metal dealer where he explained about aerocon bricks. They were porous and the right weight for my project he was kind enough he gave single piece 2ft x 8in x 8in block for this build.
Bought some aluminum square section channel with a sort of C- provision.
Used hacksaw blades to cut the brick was quite easy to cut took about 20mins in total to make 2 cuts, Fairly easy right? I know how my hands felt after cutting.
Enough of typing some eye candy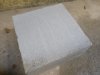
The cut section of aerocon brick
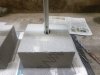
Then the brick is drilled to accommodate the aluminum channel.
*Note use only concrete drill bits and use ample water to keep things cool.
Then using spirit level and set square align the aluminum channel perpendicular to the surface.
Now the messy part
Get cement some sand and water
Mix in 1:2 ratio one part of cement and 2parts of sand
Add water until proper consistency.
Now fill in the drilled gaps with the mortar you made seal the rear parts of the aluminum channel and block before filling in gaps. I'll say the reason below.
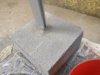
Will look something like this after a 24hrs curing.
Make the block wet always using generous amount of water.
This ensures high yield strength and less cracks in the filling.
Makes sure the stand won't wobble or shake in upcoming years.
Then using Silicon carbide sand paper of 200-220 grit would the whole block making the coarse surface soft to touch.
The use silicon carbide block to make sure surface is trued.
Let things cure for two days add generous water to the block this will make sure the block and cement gets cured properly.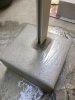
Now remove the bottom seal you made while filling the mortar. This will provide path for wires for the speakers.
Now get a 3x3x1 inch cardboard box cut to make a mold to hold the support block.
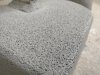
Just a closer look on the surface finish after sanding.
Will look porous yet soft and smooth for touch.
Now for the support block construction
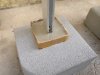
The cut cardboard box will be the mould for the support block which is just glued with hot glue to prevent water leakage from concrete during curing.
Let it set for 24 hours and cure for two days.
Again sanding with finer grit sandpaper and carbide block will make things more smooth.
Clear and transparent
To make the surface more strong and chipping resistant I used Asian paints tile guard clear.
Which is a white paint like thing dries clear.
Is water-repellent and makes the surface more resistant to physical abuse.
Makes the cleaning more easy.
Let things dry up for a day, Then second coat the whole block.
Let there be light
Bought some warm white 5050 LED strip (requirements vary on the stands height)
Install the LED strip in the aluminum channel in-between the channel provision.
Wire things appropriately.
Fetch some high quality speaker wires pull through the alumimum box channel.
Get pair of ball socket speaker wall mount to mount the speakers to the aluminum channel.
Bend a aluminum plate to house the ball socket joint, such that it links aluminum channel and the ball socket joint.
Creativity matters here and metal working experience helps in these.
So the outcome:
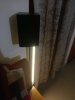
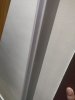
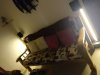
After building a DIY optical 5.1 channel receiver (please make sure to check out my entire build on the DIY section). I'll add this build plans for you guys if you wish to build similar ones.
So without much into let's jump into the build...
The quest continued as I needed a floor stand to properly install my rear surround channel as my living room wasn't planned to house surround speakers including wiring.
Went on for nearby shops the starting price for stands were about 600-700 per stand.
I felt for that price the build and quality could have been better and my speakers were quite heavy for the given small dimensions. It weighs around 600-700grams being just a 3inch and a tweeter with heafty two way diy crossover.
Mine wasn't well balanced on those stands. The stand shakes and it's barely standing a slight touch could tip things over.
So thought of building my own
The idea bulb was lit:
Saw some YouTube videos where I came across some decent builds
So with a simple build idea I went on to local metal scrap place.
And calculated the price of required Stainless steel channels
It came out to be a costly option and seems to be pretty hard to work with as I need to get things welded(again having a small welding machine, but lazy to work with).
So thought why not to use something light yet string and balance the speakers properly.
The Discovery:
Yes,The discovery CONCRETE!!!!!
Went to a nearby restaurant where I saw raw finished concrete brick wall finished with varnish.
So got the idea of having concrete as my base and aluminum as stands.
Went to nearby construction blue metal dealer where he explained about aerocon bricks. They were porous and the right weight for my project he was kind enough he gave single piece 2ft x 8in x 8in block for this build.
Bought some aluminum square section channel with a sort of C- provision.
Used hacksaw blades to cut the brick was quite easy to cut took about 20mins in total to make 2 cuts, Fairly easy right? I know how my hands felt after cutting.
Enough of typing some eye candy
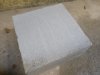
The cut section of aerocon brick
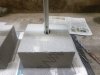
Then the brick is drilled to accommodate the aluminum channel.
*Note use only concrete drill bits and use ample water to keep things cool.
Then using spirit level and set square align the aluminum channel perpendicular to the surface.
Now the messy part
Get cement some sand and water
Mix in 1:2 ratio one part of cement and 2parts of sand
Add water until proper consistency.
Now fill in the drilled gaps with the mortar you made seal the rear parts of the aluminum channel and block before filling in gaps. I'll say the reason below.
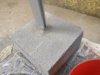
Will look something like this after a 24hrs curing.
Make the block wet always using generous amount of water.
This ensures high yield strength and less cracks in the filling.
Makes sure the stand won't wobble or shake in upcoming years.
Then using Silicon carbide sand paper of 200-220 grit would the whole block making the coarse surface soft to touch.
The use silicon carbide block to make sure surface is trued.
Let things cure for two days add generous water to the block this will make sure the block and cement gets cured properly.
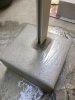
Now remove the bottom seal you made while filling the mortar. This will provide path for wires for the speakers.
Now get a 3x3x1 inch cardboard box cut to make a mold to hold the support block.
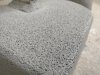
Just a closer look on the surface finish after sanding.
Will look porous yet soft and smooth for touch.
Now for the support block construction
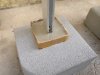
The cut cardboard box will be the mould for the support block which is just glued with hot glue to prevent water leakage from concrete during curing.
Let it set for 24 hours and cure for two days.
Again sanding with finer grit sandpaper and carbide block will make things more smooth.
Clear and transparent
To make the surface more strong and chipping resistant I used Asian paints tile guard clear.
Which is a white paint like thing dries clear.
Is water-repellent and makes the surface more resistant to physical abuse.
Makes the cleaning more easy.
Let things dry up for a day, Then second coat the whole block.
Let there be light
Bought some warm white 5050 LED strip (requirements vary on the stands height)
Install the LED strip in the aluminum channel in-between the channel provision.
Wire things appropriately.
Fetch some high quality speaker wires pull through the alumimum box channel.
Get pair of ball socket speaker wall mount to mount the speakers to the aluminum channel.
Bend a aluminum plate to house the ball socket joint, such that it links aluminum channel and the ball socket joint.
Creativity matters here and metal working experience helps in these.
So the outcome:
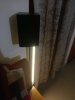
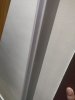
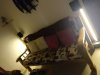