Hi Friends
From past 10 days, I have been doing this project in parallel with my other projects. I role is to only make the "finished enclosures" and then they will be shipped to the respected owner.
In past 10 Days I have completed the drawing, made cutting layout, and had the baffles cutting done on CNC router. And right now they are undergoing assembly.
I have used 24 mm Birch Ply for front and back and for rest of sides 18 mm Birch ply is used. The internal dimensions are matched as per the original enclosure made from MDF with has 30 mm Front & rest all sides 22 mm MDF.
Enough of right up, for details you can click on the below link for more details like Drivers and crossovers.
Tapered Quarter Wave Tube
Now I am sharing the photos of the work done till now.
All cutting is done on CNC router except for the 45 Deg joints. They are done with hand held circular saw.
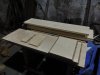
When you have other project running in parallel you don't focus on taking photos, In the above photo of cut pieces, some are missing as the assembly was already started.
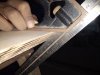
Checking the 45 Deg Cut Right angle which also has a provision to check 45 Deg Cuts.
When you have the perfect 45 Deg Cut, it reflects the same during assembly, see the matching of this joint in below photo.
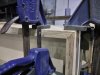
Now sharing some random photos of assembly
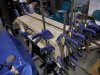
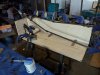
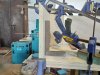
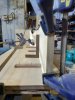
Further i have to cut the degree of the tapered tube (baffle), for which i had used by router with degree attachment. It was as easy as (kaato-ghoolo aur lagao---- lol)
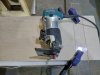
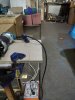
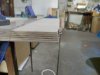
In below photo a brace is being glued & clamped with tapered baffle, Everything is glued no screws, it will be left overnight today for drying.
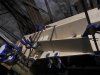
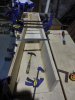
I will keep on updating this project also.
Sadik
From past 10 days, I have been doing this project in parallel with my other projects. I role is to only make the "finished enclosures" and then they will be shipped to the respected owner.
In past 10 Days I have completed the drawing, made cutting layout, and had the baffles cutting done on CNC router. And right now they are undergoing assembly.
I have used 24 mm Birch Ply for front and back and for rest of sides 18 mm Birch ply is used. The internal dimensions are matched as per the original enclosure made from MDF with has 30 mm Front & rest all sides 22 mm MDF.
Enough of right up, for details you can click on the below link for more details like Drivers and crossovers.
Tapered Quarter Wave Tube
Now I am sharing the photos of the work done till now.
All cutting is done on CNC router except for the 45 Deg joints. They are done with hand held circular saw.
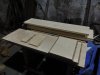
When you have other project running in parallel you don't focus on taking photos, In the above photo of cut pieces, some are missing as the assembly was already started.
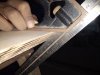
Checking the 45 Deg Cut Right angle which also has a provision to check 45 Deg Cuts.
When you have the perfect 45 Deg Cut, it reflects the same during assembly, see the matching of this joint in below photo.
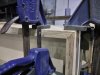
Now sharing some random photos of assembly
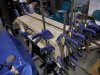
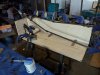
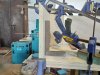
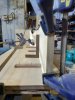
Further i have to cut the degree of the tapered tube (baffle), for which i had used by router with degree attachment. It was as easy as (kaato-ghoolo aur lagao---- lol)
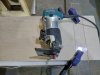
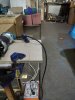
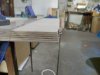
In below photo a brace is being glued & clamped with tapered baffle, Everything is glued no screws, it will be left overnight today for drying.
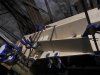
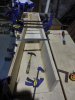
I will keep on updating this project also.
Sadik